Tomiyasu Metal Printing Co., Ltd.
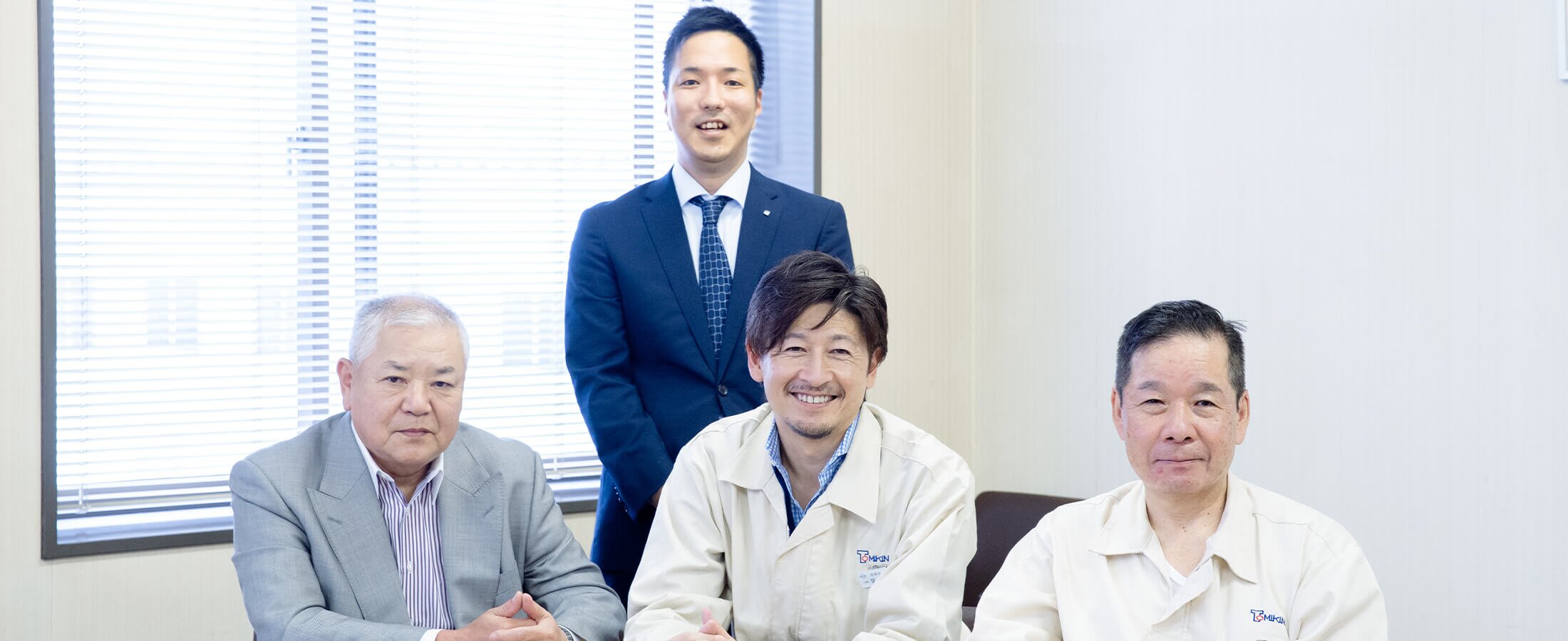
One of Japan’s top metal printing manufacturers
which owns all of FUJI KIKAI KOGYO’s metal printing machine models
Tomiyasu Metal Printing is one of Japan’s top metal printing manufacturers, which owns all of FUJI KIKAI KOGYO’s metal printing machine models. Through printing on and manufacturing tinplates and other metal plates as well as work involved therein, they express the “creation of color” and “culture of color,” striving to reproduce color as close to nature as possible and endeavoring to expand the colors that humans can express.
Metal printing machine
H.K
Tomiyasu Metal Printing Co., Ltd.
Vice-president and Representative Director
K.K
Tomiyasu Metal Printing Co., Ltd.
Director and Plant Manager
K.O
Tomiyasu Metal Printing Co., Ltd.
Director and Deputy Plant Manager
N.O
FUJI KIKAI KOGYO Co., Ltd.
Metal Printing Machine Department Sales Member
INTERVIEW
Contents
Reliability, safety, and operability unique to Made-in-Japan products
N.O
Could you tell us when you installed our metal printing machines?
H.K
I recall that we started using them in the late 1970’s. Among the equipment we have currently, there is a machine that was made in 1988, so we have a relationship that has lasted over 30 years. We first connected with FUJI KIKAI KOGYO through our relationship with DIC Corporation, a Japanese metal ink and paint manufacturer, which led us to today.
N.O
What made you decide to install our products?
H.K
Since you have been manufacturing and selling rotogravure printing machines since the 1970’s and metal printing machines since the 80’s, your products have reliability and safety as Made-in-Japan products, and also have outstanding operability, which were big points for us.
As a company dedicated to metal printing, we are particularly committed to carrying out beautiful printing which utilizes the reflection effect from the surface. With that in mind, I believe your company really understood our feelings at that time and provided a device that met our needs.
Reducing operator burden and improving workability and quality Revolutionary equipment development for printing machines
N.O
In the many years you have used our products, was there any event that left an impression on you in particular? What was it?
K.K
The dampening solution in metal printing machines used to use a fabric sleeve called a molleton roller. In the past, we would change the ink color almost every day. When the fabric sleeve got dirty, the assistants would wash it by hand using faucet water, washing it by hand even in the cold winter, and after work, it would be difficult to get the color off our hands. It was a lot of trouble. However, when the linked solution supply device was developed, it reduced the burden on the operator, bringing about a revolutionary improvement to workability and quality. It was a groundbreaking piece of equipment for printing machines at the time, and all existing machines were improved quite quickly.
Sweets, coffee, seaweed, canned food... Metal containers can be found throughout daily life
N.O
Currently, what kinds of products, specifically, are made using our company’s printing machines?
K.O
We make metal containers including general cans, food products, canned foods, oil cans, bottle tops, and caps. These are products that everyone sees and uses in their daily lives, such as cans for sweets, seaweed, or tea, cans for coffee, fruits, or fish, pails, and bottle caps.
N.O
Precisely because these products are used throughout daily life, you feel the need to thoroughly ensure technical power and safety in the future.
K.K
As the S (for short) in P453S shows, it cuts down on space, allowing us to install the machine in the line configuration we desired.I believe it would have been difficult to install the machine at the conventional machine length. Also, the inking alignment was changed to improve the balance of ink and water. This shortened the amount of time required for color matching until printing is stabilized, thus successfully improving productivity.
The quality required from products is increasing every year, so moving forward, we are looking forward to seeing designs, improvements, and new efforts from you that meet the needs of the era.